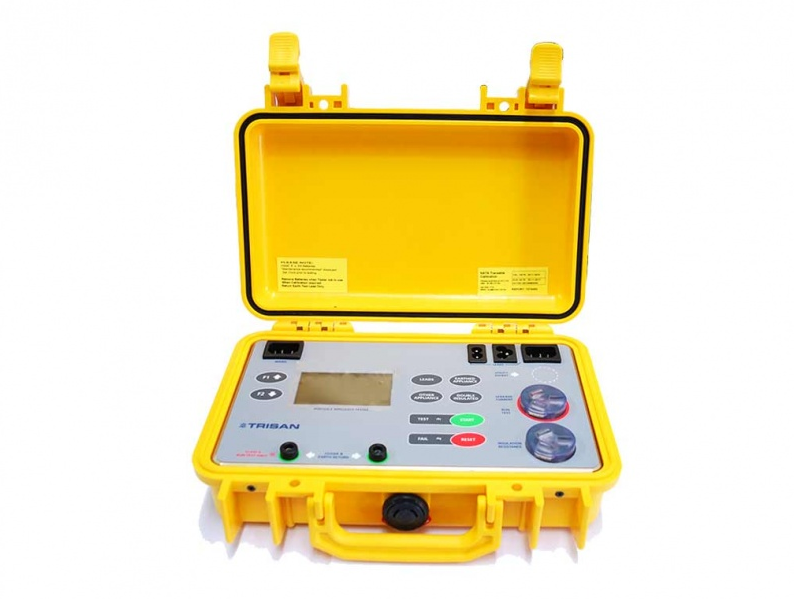
Electrical Testing & Tagging
What is Test & Tag?
Test and Tag is the name given to the process of checking the safety of portable electrical appliances.
It involves two parts: first visually inspecting the appliance for any damage, followed by electrically testing it with a Portable Appliance Tester.
Once tested, the item is placed with a tag to confirm that it has in fact been tested, along with showing who tested it, the test date and when the next test is due.
The primary reason behind doing testing and tagging is to ensure the safety of the people coming into contact with the appliance, while also minimising the risk of an electrical hazard.
Who needs Test & Tag?
Industries such as construction, demolition and mining are required to have their appliances tested and tagged every 3 months. This is because of the harsh nature of the industry which is likely to damage equipment at a
faster rate.
For each 3 months of testing, the test and tag colours will change for different periods throughout the year, which effectively make certain months coincide with a specific test tag colour. With the exception of these industries, testing and tagging is not a legislative requirement for other workplaces.
However, the employer does have a duty of care to ensure the safety of its employees, meaning that if someone
was hurt from an appliance that wasn’t tested and unsafe, they could be found liable.
Because of this, it’s the employer’s responsibility to have all portable electrical appliances tested.
For people in the hire industry, there are some minimum requirements. For instance, before equipment is hired out it needs to be visually inspected by the hirer before every lease. The actual appliance needs to be tested also every 3 months, which is the hirer’s responsibility when they have possession of it.
Test & Tag intervals
For the most common environments, we recommend the following frequencies:
3 months: building, construction and demolition – this requires the most frequent testing due to it being considered a harsh environment and therefore an appliance being damaged is more likely compared to other settings.
6 months: factories, warehouses and production – this type of an environment isn’t considered as harsh, but because appliances are often used constantly it needs to be tested every 6 months.
12 months: an environment where the equipment/supply cord is prone to flexing or open to abuse – this is often referred to as a hostile environment as the appliance can be overused and is therefore exposed to abuse by the user, as well as dust, general deteriation and the weather.
5 yearly: an environment where the equipment/supply cord is not prone to flexing or open to abuse – this is commonly referred to as a non-hostile environment – a typical example of this might be a company’s server room.
First Aid Training
Nationally Recognised 'Statement of Attainments' partnered with ABC First Aid RTO 3399
Emergency Evacuation Diagrams
Stay compliant with Emergency Evacuation Diagrams designed by Wagga Workplace Safety